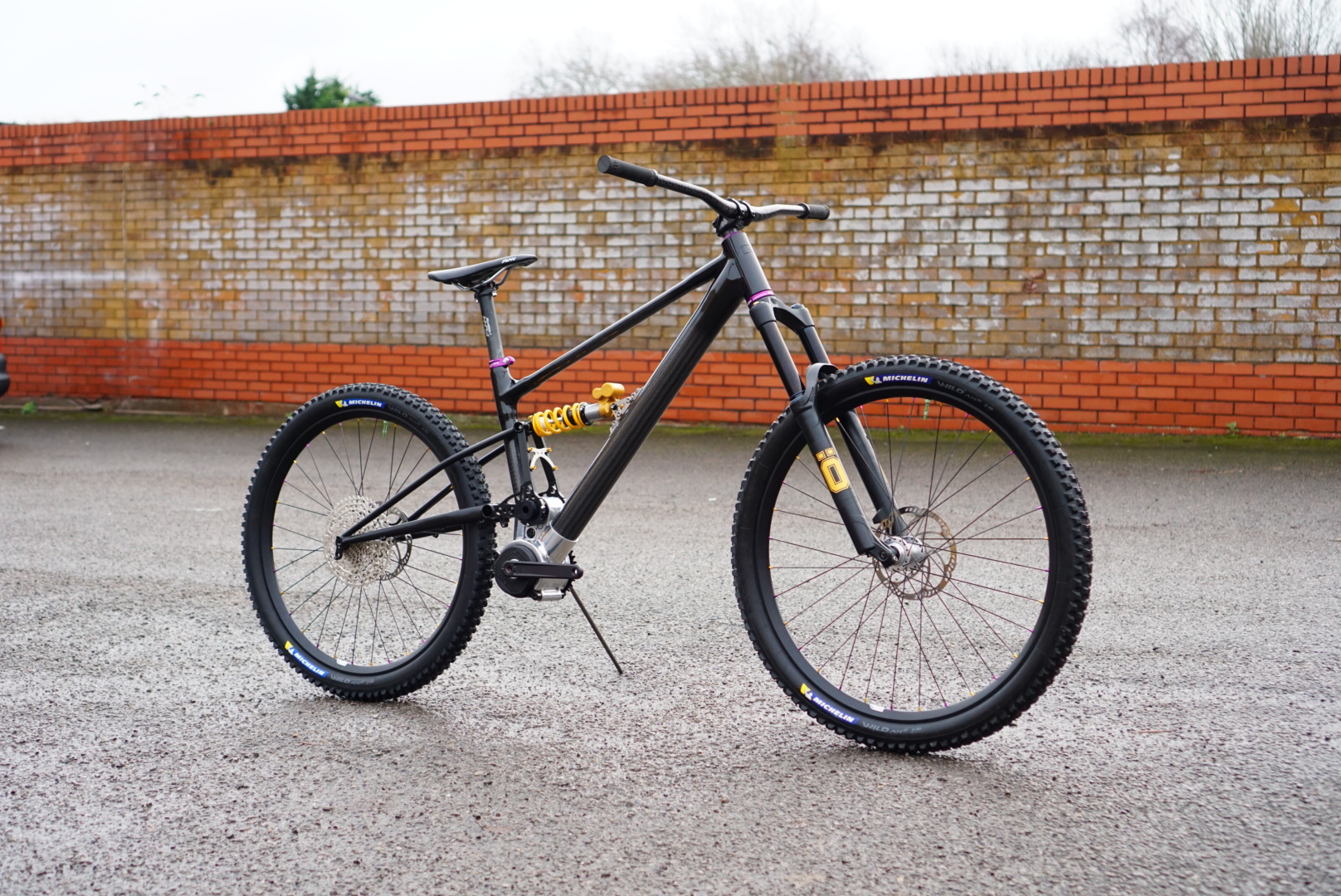
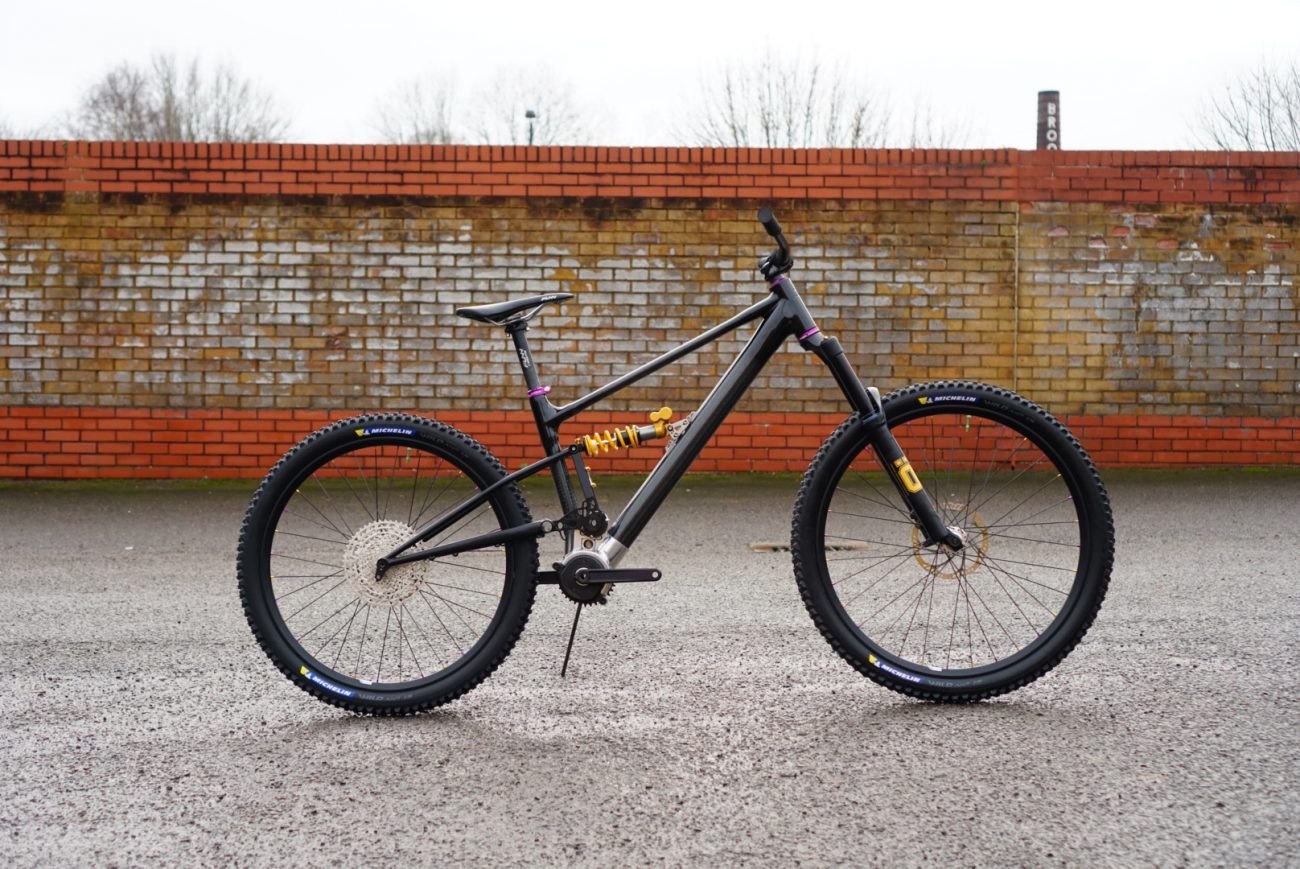
Ladies and gents, presenting Starling Cycles’ first carbon fibre full suspension mountain bike frame, or more specifically eMTB frame.
… But before you get too excited, read on. There’s a little more to it.
As many of you may know I (yep, it’s me, Joe McEwan, founder of Starling Cycles) had a previous life as an Aerospace Engineer, with many of my years of experience focussing on R&D for Carbon Fibre structures.
Old habits die hard, and when we had the opportunity to work on a project with the National Composite Centre (where I had previously worked as Technical Lead for GKN who were a partner), it was difficult to refuse.
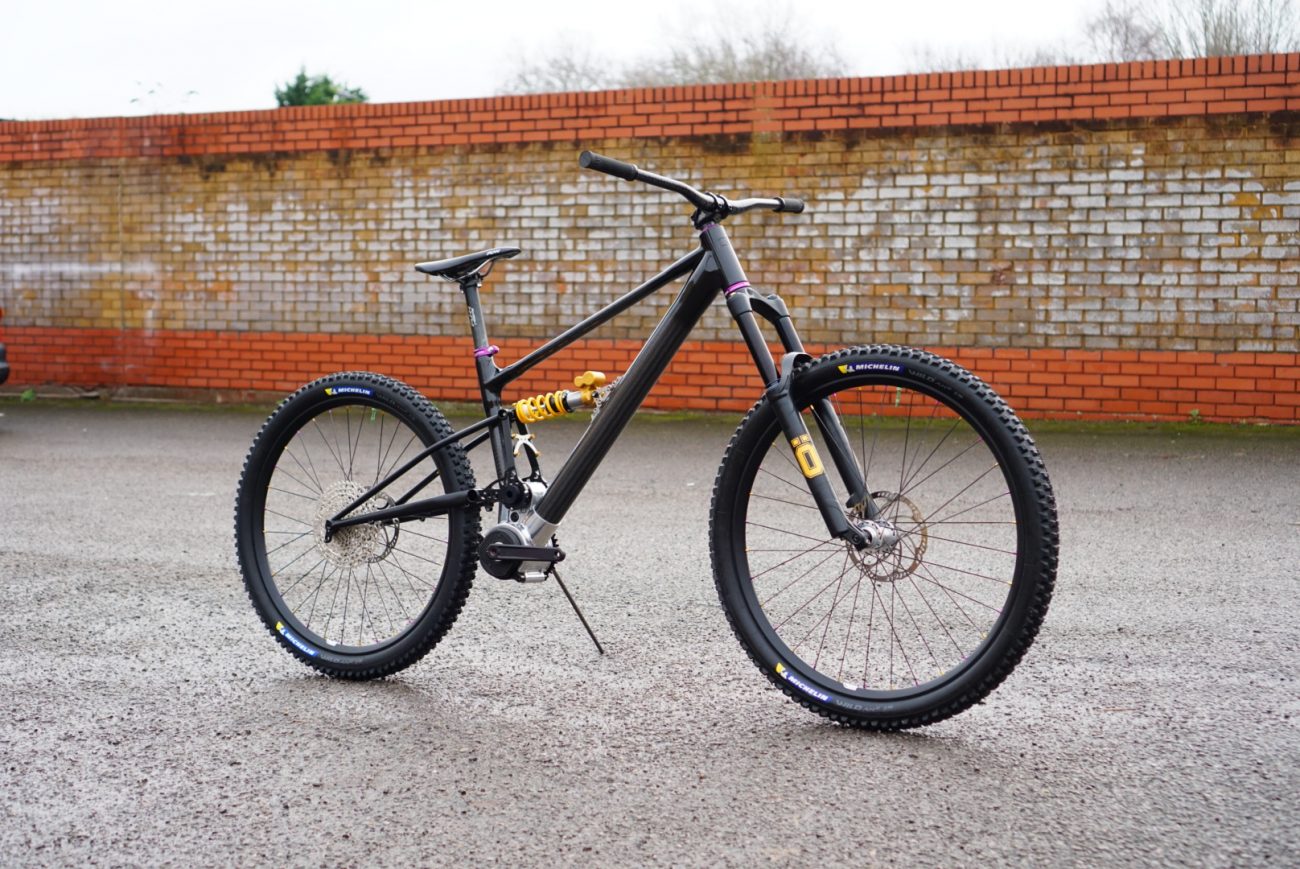
But wait a minute, doesn’t Starling only makes steel bikes? And didn’t I always say carbon bikes are rubbish?!
Yes, we only make steel bikes. But no, I never said carbon is rubbish, it’s just that having worked in aerospace and seen carbon manufacture to the highest level, I don’t believe current carbon manufacturing methods for bikes offer anywhere near the kind of quality I’m used to.
But this project offered an opportunity to try and change that… So why not?
The idea of the project was to use braided thermoplastic tubes with novel design lugs. The thermoplastic has several advantages over traditional epoxy-based carbon fibres:
- Firstly, thermoplastic is much tougher against impact damage than epoxy. Many people are not aware, but with an epoxy composite you can take an impact that shows no damage on the outside, but there could be significant internal damage within the laminate that risks the integrity of the structure. This is not a problem with thermoplastic based composite where the internal damage is much less likely to occur due to high plasticity of the material.
- Secondly, the thermoplastic can be reformed, which means it is much more amenable to repairs. Whereas epoxy is quite often restricted to ‘cosmetic’ repairs.
- The ability of the thermoplastic to be reformed means that, although it can’t be recycled (I’ll come onto this in a moment) it can be repurposed in a much easier way. For example, old frames could be returned to the manufacturer and the tubes cut out and reformed into a smaller frame size. Theoretically, you could heat up a thermoplastic composite and remove the plastic matrix and retrieve the carbon fibres. But realistically, this would use significant amount of energy and reduce the properties of both materials.
- As an aside, we need to be super careful when using the term, ‘recycled’, to me it is a cycle than can continue for ever. Steel for example, can be recycled. It can infinitely be melted down and reformed into pristine new material. Noting some super high grade steel do require pristine ore.
- Plastic cannot be recycled, there is always a degradation in quality with each cycle. The life may only be three or so cycles. This is not recycling, just reusing.
- Epoxy Carbon fibre can never be recycled, as much as some people will try to tell you it can. Currently, as best it can be chopped up and maybe used as filler in short strand plastics. Mostly it is chopped up and used a filler, or mug coaters. And this one short reuse with much degraded qualities is about as far as you can go.
- Thermoplastic composite require much less energy to manufacture than epoxy composites. The time to heat for epoxies to cure and therefore the energy requirements are much more.
- The solution being worked on also offers significant quality benefits and ability for mid-process inspection. This means manufacturing scrap rate will be significantly reduced. I’ve heard up to 50% for some epoxy carbon frames, i.e. the piles of frames going into the sea we have all seen.
Because of the above points: tougher, repairable, re-useable, lower energy to manufacture, better manufacturing quality, thermoplastic carbon frames present a much less environmentally damaging solution for bike frames than epoxy-based carbon frames.
So, with all these benefits, the project looked to develop a new high volume, low cost, high-quality manufacturing process for carbon fibre bike frames. We made significant process and built a beautiful looking eBike frame. It used a Freeflow technologies motor system, sitting within a machined aluminium motor casing, this region was too tricky for the carbon process at such early stages. It also had a jack drive system like our Sturn DH bike and a steel swingarm to get all the compliance and grip that Starlings are famous for. There were also a few other little treats such as a 3D printed stainless steel shock mount.
So the bike looks great, but the manufacturing process for the lugs didn’t work out quite as we planned and we didn’t come up with a solution we were fully happy with.
I’d love to go into the details, but there are some pretty clever and novel ideas that I’d prefer to keep to myself! Going forward we are working with the NCC to perform more studies to refine the technology. In the meantime, 76Projects stepped in and produced some 3D printed lugs to allow us to build the mock-up bike.
Going forward we have more studies happening to refine the technology. It’s a long way off being a finished bike, or even being rideable, but it was a super interesting project.
We’re not quite there yet, but it’s exciting stuff!
You can read more about this over on CompositesWorld.com.
Thanks to the National Composites Center, Composite Braiding Bristol, 76Projects and Freeflow Technologies.